// Coolant Flushing System
Key Requirements
Portability:
The system must be portable, enabling it to be easily moved and securely docked within the machine during operation.
Multi-Functionality:
The system must allow the operator to seamlessly switch between three operational modes:
– Flushing
– Emptying
– Cleaning
Performance:
The system must deliver a consistent flow rate of approximately 120 litres per minute.
Coolant Compatibility:
All components of the system must be constructed from materials that are fully compatible with and resistant to the coolant used in the machines.
Design and build a robust, user-friendly coolant flushing system that meets the specified performance and functional requirements, ensuring ease of operation and long-term reliability in the manufacturer’s environment.
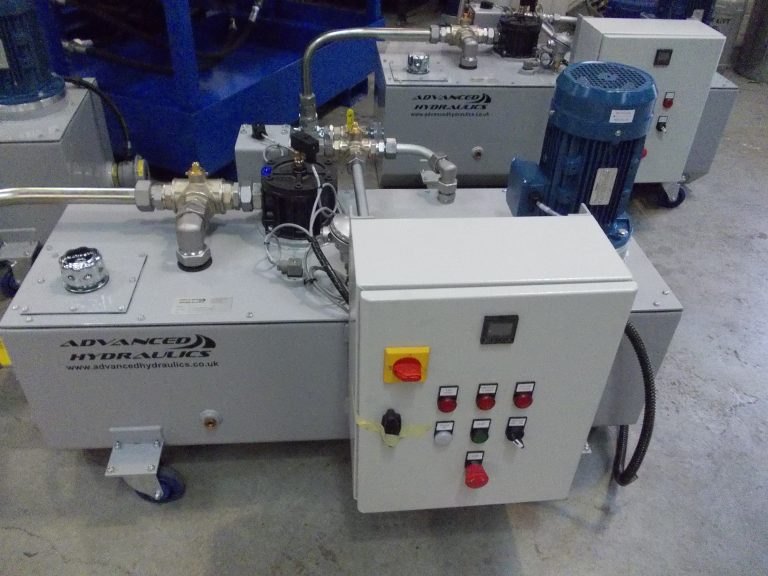
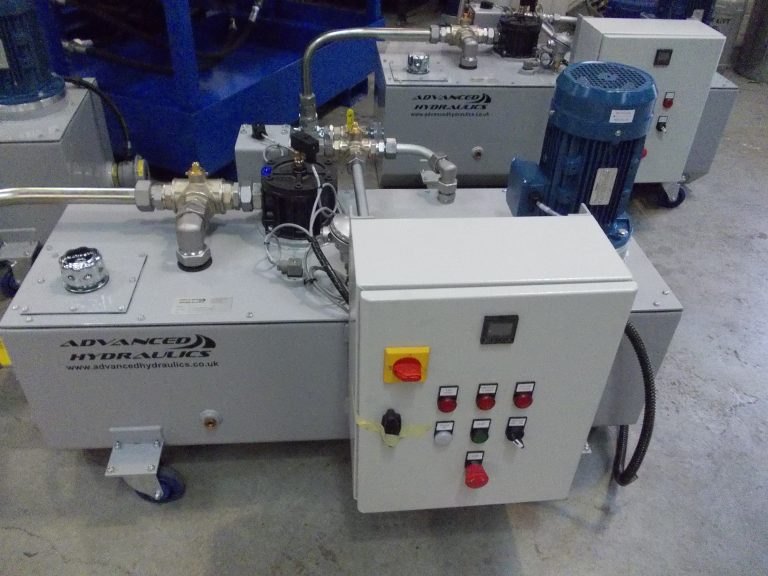

Design:
The mobile coolant system has been designed with a 300-litre capacity tank made from carbon steel. This choice of material ensures durability and resistance to corrosion, which is crucial for maintaining reliability in industrial environments.
To power the system, we selected a cast iron gear pump. This pump is designed to deliver approximately 110-120 litres per minute ensuring efficient performance and consistent coolant flow under various operational conditions.
For flow management, the system includes a manual diversion mechanism that allows flexible control over the pump’s delivery. The coolant is routed through both suction and delivery filtration systems, which are designed to be cleaned periodically. This feature helps maintain optimal performance and prevents clogging.
The electrical control panel integrates essential functions such as stop, start, isolate, and an emergency stop. It also features warning lights for ‘Filters Clogged’, ‘Low Fluid Level’, ‘Heater On’, and ‘Running’, providing clear indicators of the system’s status. An independent ‘On/Off’ switch for the heater is included to enable pre-heating of the coolant as needed. Additionally, the panel is equipped with a digital temperature readout controlled by a PID controller to precisely monitor and maintain the coolant temperature.
To ensure effective operation, an immersion heater with an integral thermostat is incorporated into the design. This heater pre-heats the coolant, allowing the system to reach and maintain the optimal temperature for efficient performance.
This design process emphasizes creating a robust and user-friendly mobile coolant system with comprehensive control and monitoring features, meeting the high standards required for industrial applications.
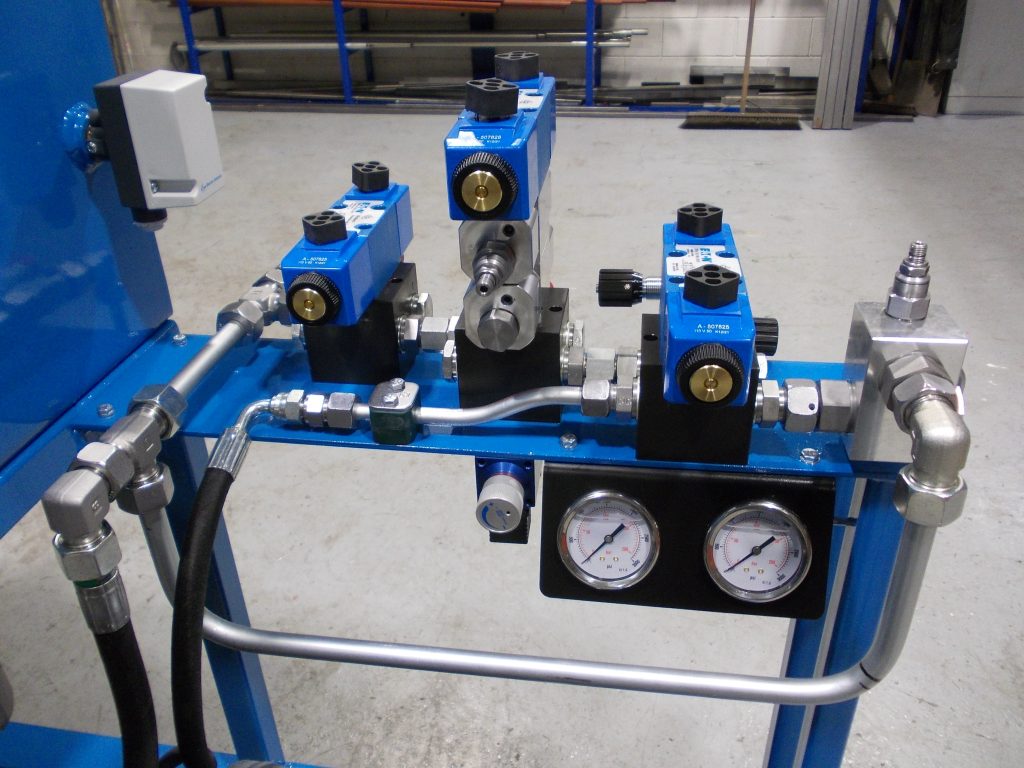
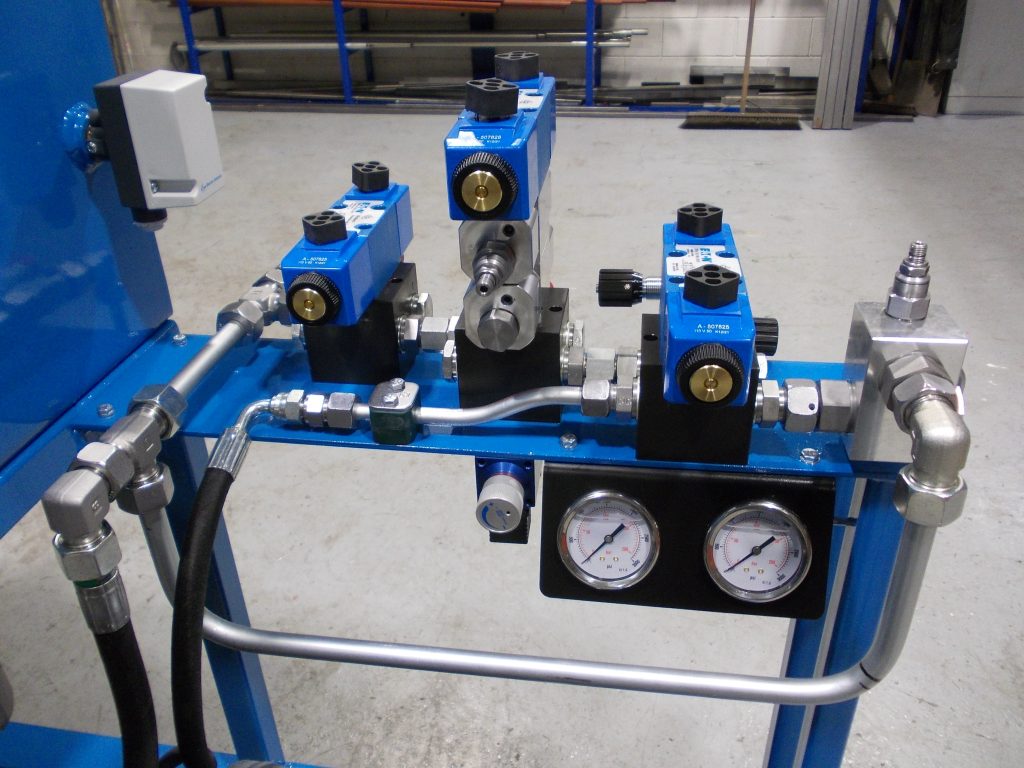
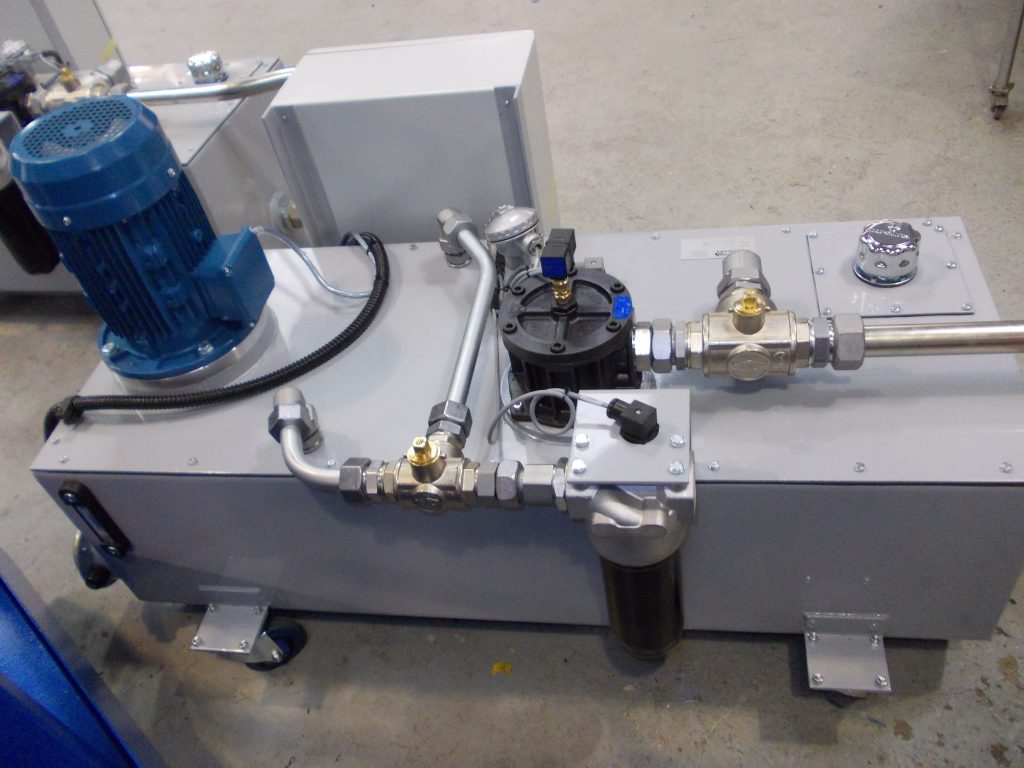
Manufacture:
The manufacturing process for the 300-litre mobile coolant system began with the fabrication of a carbon steel reservoir, which was then mounted on castors. This design feature allows for easy mobility and positioning of the system within operational environments.
A high efficiency electric motor was installed, driving a cast iron pump capable of delivering 110-120 litres per minute. The system included a manual diversion feature to allow flexible control of the pump delivery.
To maintain fluid purity and system efficiency, suction and delivery filters were integrated, designed for periodic cleaning.
An electrical panel was mounted on the tank and fully wired to interface with all system components. This panel features controls for starting, stopping, isolating, and emergency stopping the unit, along with indicator lights for ‘Filters Clogged’, ‘Low Fluid Level’, ‘Heater On’, and ‘Running’. An independent switch was included for controlling the heater.
An immersion heater with an integral thermostat was fitted, with an interlock to prevent activation when coolant levels are low, ensuring safe and efficient pre-heating.
Overall, the design integrates reliable components and practical features to ensure efficient operation, ease of maintenance, and operational flexibility.
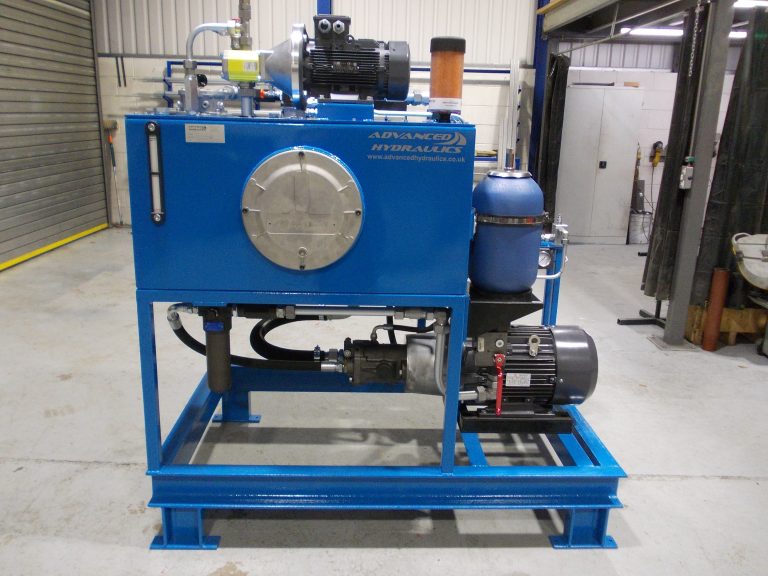
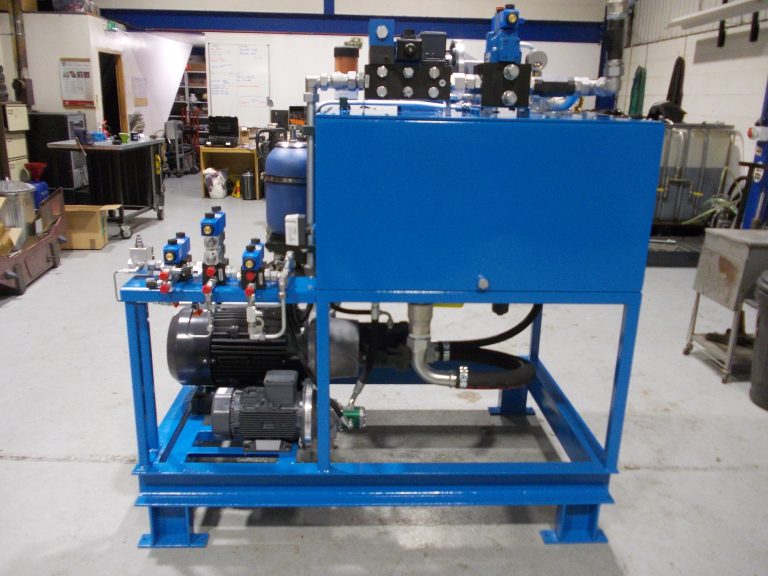
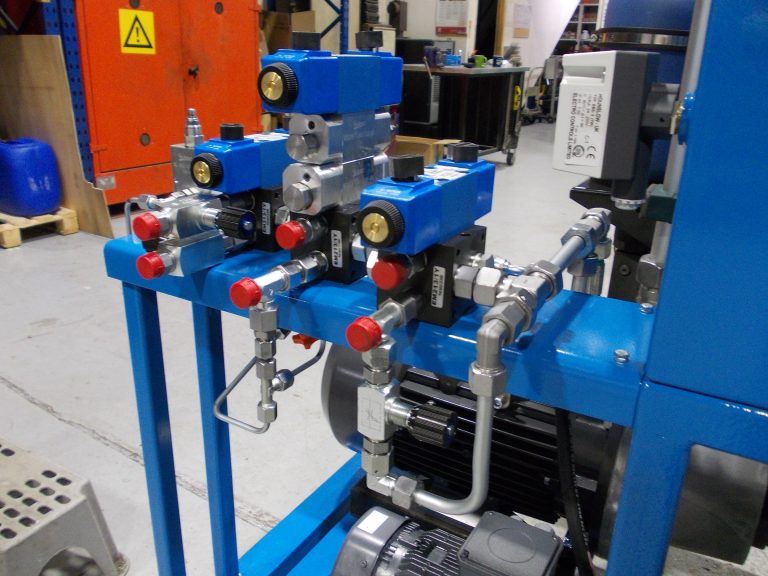